

3 Steps to perfect application
-
☑️ Finalise your choice
Choose the appropriate size and colour for your project. Need help choosing? Our friendly team are here to help - contact us!
-
☑️ Order your chosen product
Once you've finalised your order head to the checkout to complete your purchase. Your order will be dispatched within 24-48 hours.
-
☑️ Apply your product with ease
Our easy-to-use formulas make application a breeze. Follow the manufacturer's instructions for a flawless finish.
Why choose Antel for your flooring products?
At Antel, we're your one-stop shop for all your building chemical needs. Here's why you should choose us:
-
🌟 Unmatched expertise
We have over 20 years of experience in formulating and manufacturing high-performance building chemicals.
-
👍 Superior products
Our floor paints,anti-slip adhesives, andfloor screedsare designed for easy application, long-lasting durability, and a minimal environmental footprint.
-
🚀 Fast delivery
Get your project started quickly! Most orders are dispatched within 24-48 hours for fast delivery within the UK

★★★★★ Next Level Flooring
British Airways Hangar
Used this heavy-duty paint at the British Airways hangar—excellent coverage, tough finish, and built to withstand heavy use. Perfect for industrial environments. Highly recommended.
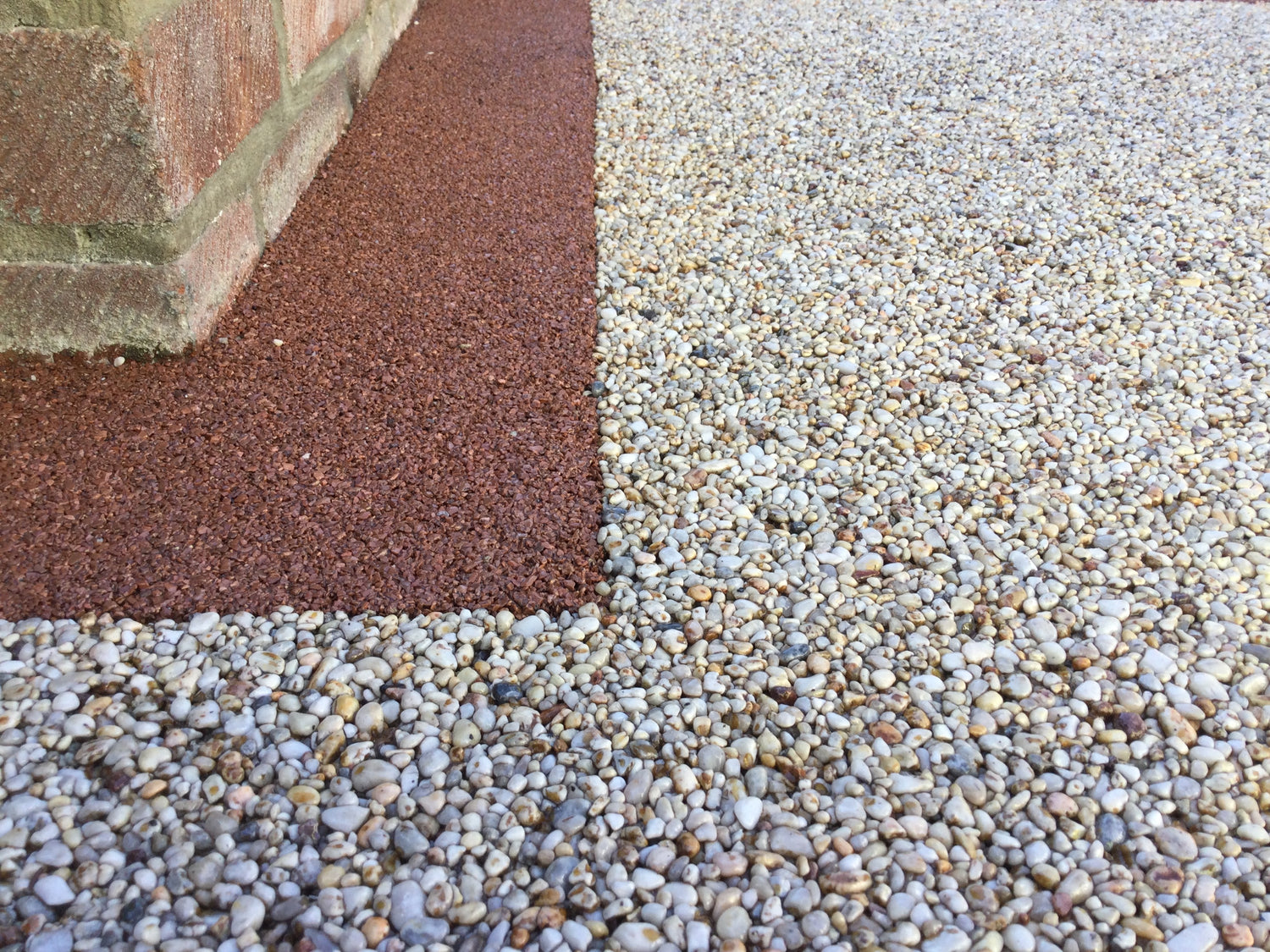
★★★★★ Mr Ian R
Very happy!
I am very happy… the small stones are now bonded together, and another coat would be too much as I would loose the grip on the patio that the children play on. Thanks for your help and advice on selecting the right product.
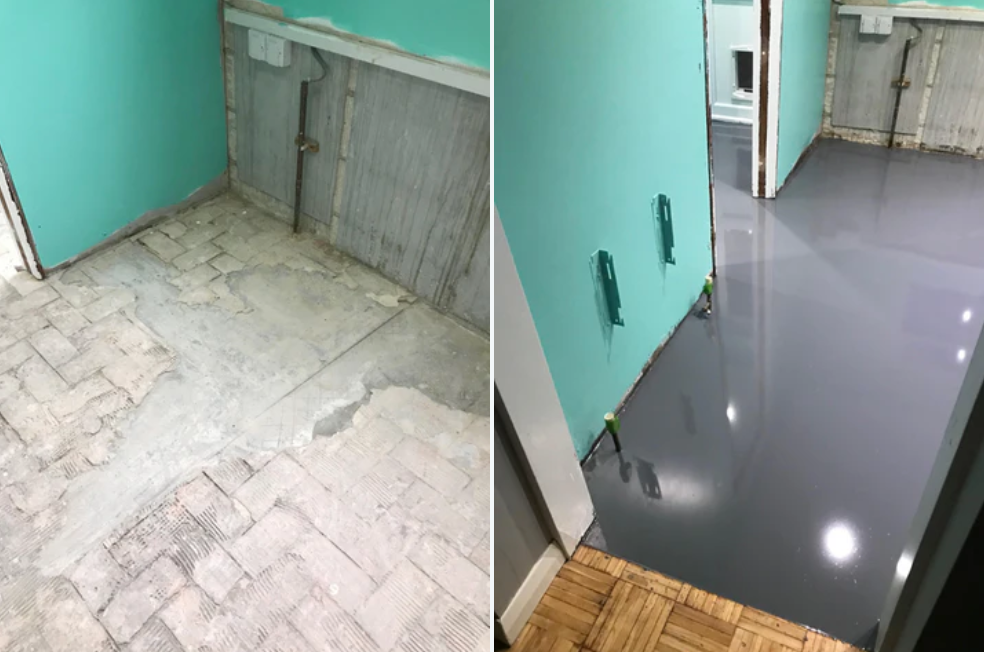
★★★★★ Mr John S
Extremely pleased
The instructions from Julian and recommendations in regards to tools and laying the flooring were invaluable and enabled me to achieve a showroom like finish which i am extremely pleased with.
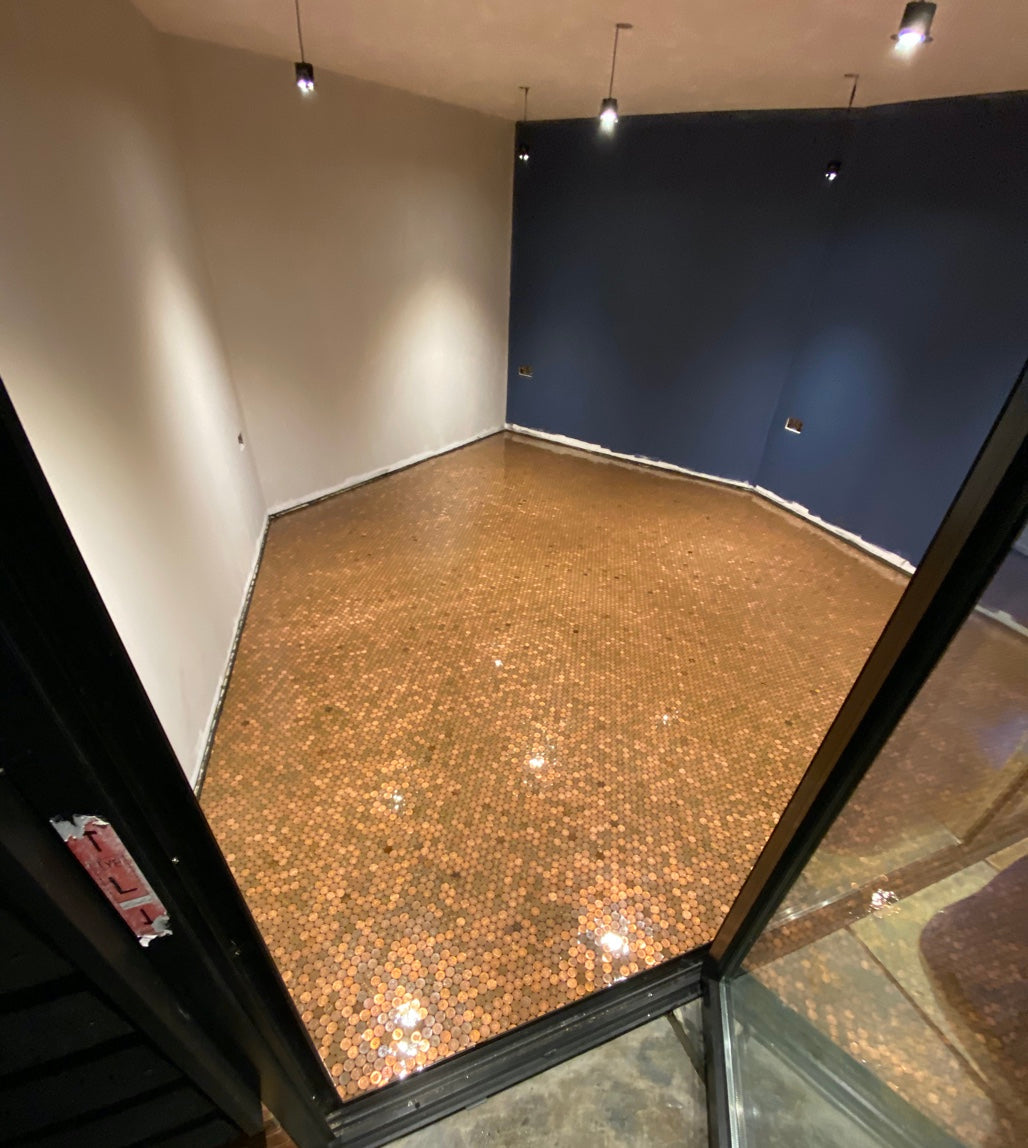
★★★★★ Mr Ross J
Looks great
Just wanted to say thanks for helping me out with the resin products, it was the perfect quantity and looks great.
Fast Set Solvent-Free Epoxy Coating Applied to The Shard’s Stairway for Rapid Refurbishment
Heavy-Duty Epoxy Coating Revitalises the Floor of Marwell Zoo’s Tropical House
Antel Epoxy Resin Enhances the Refurbishment of Gunwharf Linkspan Bridge
Antel Self-Smoothing Floor Screed and Epoxy Coating Applied in The Fisheries, London
Antel Epoxy ClearCoat Resin Enhances British Airways Lounge Refurbishment at Heathrow
Antel Water-Based Epoxy Floor Paint Applied at London Cakes
FAQs
What makes Antel's flooring products different?
Our products are formulated with over 20 years of experience for superior ease of use, long-lasting durability, and minimal environmental impact.
How do I choose the right flooring solution for my project?
We offer a wide selection! Our dedicated technical team is happy to answer your questions and help you find the perfect product for your specific needs. Feel free to contact us!
How fast can I get my order?
Most orders are dispatched within 24-48 hours for fast delivery within the UK (additional charges may apply). We also handle international shipping!
Can I still get help if I'm unsure during my project?
Absolutely! Our technical support team is always happy to offer guidance on proper application to ensure flawless results.
Are Antel's products environmentally friendly?
Yes! We take environmental responsibility seriously and strive to create high-performance products with minimal environmental impact.
Need some expert advice?
Our knowledgeable support team is here for you! Whether you have questions about a specific product or need help choosing the right one, we're happy to assist.